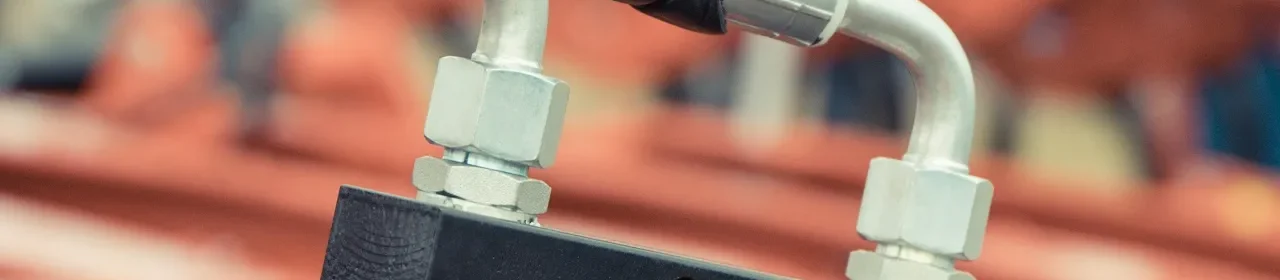
Introdução
Os retentores são componentes cruciais em sistemas hidráulicos e mecânicos, desempenhando um papel fundamental na prevenção de vazamentos e na manutenção da integridade de máquinas. Uma falha em um retentor não só pode causar vazamentos indesejados, mas também levar a uma redução significativa no desempenho e até mesmo a falhas catastróficas de equipamentos, comprometendo a segurança no ambiente de trabalho. Neste artigo, exploraremos como identificar e resolver falhas comuns em retentores, garantindo que suas máquinas operem de maneira eficiente e segura.
1. Compreender as Funções dos Retentores
Os retentores são essenciais para manter os fluidos dentro dos sistemas mecânicos e hidráulicos, impedindo a entrada de contaminantes externos que podem causar danos e desgaste. Eles são projetados para suportar diferentes condições de operação, variando conforme a aplicação em termos de temperatura, pressão e exposição a produtos químicos. A manutenção adequada e o entendimento de suas funções não apenas prolongam a vida útil dos retentores, mas também garantem que todo o sistema funcione de maneira eficaz. Afinal, um retentor bem mantido é sinônimo de menos tempo de inatividade e custos reduzidos com manutenção.
Cada retentor deve ser escolhido com base nas especificidades de sua aplicação, considerando fatores como material de fabricação e design. Materiais comuns incluem borracha nitrílica, poliuretano e PTFE, cada um oferecendo diferentes vantagens dependendo do ambiente de operação. Por exemplo, retentores de PTFE são excepcionais para aplicações em altas temperaturas, enquanto os de borracha nitrílica são preferidos em ambientes menos exigentes. A escolha correta assegura que o retentor possa oferecer a melhor vedação possível, maximizando a eficiência e a segurança das máquinas industriais.
2. Identificação Visual de Desgaste
A identificação visual de desgaste nos retentores é um método eficaz para prevenir falhas mais sérias nos sistemas mecânicos e hidráulicos. Esses componentes são cruciais para garantir a vedação e a proteção contra contaminação externa. Sinais de desgaste podem incluir rachaduras visíveis, ressecamento do material, e deformações que alteram o perfil original do retentor.
É importante realizar inspeções regulares e buscar por alterações na textura e na cor, além de verificar a presença de pequenos fragmentos de material ao redor do retentor, indicativos de degradação. Utilizar fotografias de alta resolução pode ajudar na comparação e análise ao longo do tempo, permitindo identificar padrões de desgaste antes que resultem em falhas operacionais.
3. Verificação de Vazamentos
Os vazamentos são frequentemente o primeiro sinal de que um retentor pode estar falhando. Para detectar esses vazamentos, uma abordagem sistemática é essencial. Inicie inspecionando as áreas ao redor dos retentores após a máquina operar por um período extenso, pois isso permite que qualquer vazamento se torne mais evidente.
Métodos como a aplicação de um spray de teste, que cria uma camada visível sobre o retentor, podem destacar a presença de fluidos escapando. Além disso, é recomendável a utilização de luz ultravioleta para detectar vazamentos de fluidos específicos que contêm traçadores fluorescentes. Monitorar estes pontos críticos regularmente ajuda a identificar o início de falhas, permitindo intervenções antes de ocorrerem danos maiores ou paradas inesperadas.
4. Avaliação do Ambiente Operacional
O ambiente operacional tem um impacto significativo na durabilidade e eficácia dos retentores. Ambientes com alta contaminação por partículas, variações extremas de temperatura, ou exposição a produtos químicos corrosivos exigem uma atenção especial.
Para cada cenário, os retentores devem ser selecionados com base na sua capacidade de resistir às condições específicas. Por exemplo, em temperaturas muito altas, materiais como Viton ou silicone podem ser preferíveis devido à sua resistência ao calor. Avaliar o ambiente permite não apenas escolher o material adequado, mas também planejar uma rotina de manutenção que considere as condições de operação, ajustando a frequência de substituição e inspeção para maximizar a vida útil dos componentes e minimizar falhas.
5. Testes de Pressão e Temperatura
A realização de testes de pressão e temperatura é vital para garantir que os retentores operem eficazmente sob diferentes condições de trabalho. Estes testes simulam ambientes operacionais extremos, como altas temperaturas ou pressões excessivas, que podem ser encontradas em operações industriais pesadas ou em equipamentos de mineração. A utilização de equipamentos especializados, como manômetros e termômetros de alta precisão, é essencial para medir a capacidade dos retentores de manter sua integridade estrutural e funcional nessas condições. A periodicidade desses testes deve ser definida com base na frequência de uso dos equipamentos e na severidade das condições operacionais a que são expostos.
Além disso, é recomendado o uso de câmaras de teste ambiental que podem replicar condições extremas de temperatura e pressão. Essas câmaras ajudam a identificar potenciais falhas nos retentores antes que eles sejam colocados em uso real, reduzindo assim o risco de falhas catastróficas que podem resultar em paradas não planejadas e custos de manutenção elevados. A avaliação contínua através desses testes permite que as equipes de manutenção ajustem as práticas de instalação e substituição, garantindo que apenas os retentores que passam nesses rigorosos testes sejam utilizados nos sistemas críticos.
6. Inspeção Regular e Manutenção Preventiva
A importância de uma inspeção regular e manutenção preventiva para retentores não pode ser subestimada. Inspeções frequentes ajudam a detectar sinais precoces de desgaste ou danos, o que é crucial para prevenir falhas no sistema e evitar paradas de máquinas dispendiosas. Durante essas inspeções, é importante verificar a presença de rachaduras, endurecimento, desgaste irregular ou qualquer sinal de deterioração que possa comprometer a eficiência do retentor. Estabelecer um cronograma regular de inspeções com base nas recomendações do fabricante e nas condições específicas de operação de cada máquina é uma prática recomendada que assegura a integridade contínua dos componentes.
Além das inspeções, a manutenção preventiva inclui também ações como a limpeza adequada dos retentores e a aplicação de lubrificantes apropriados, quando necessário. Este plano de manutenção deve ser detalhado e seguido rigorosamente para garantir que todos os componentes funcionem de maneira ótima. A implementação de um plano de manutenção proativo não apenas prolonga a vida útil dos retentores, mas também melhora a segurança e a eficiência operacional das máquinas. Assim, as equipes de manutenção podem antecipar problemas potenciais e programar intervenções antes que falhas graves ocorram, otimizando a operação e reduzindo custos a longo prazo.
7. Troca e Atualização de Retentores
A substituição de retentores é uma etapa crítica na manutenção de sistemas hidráulicos e mecânicos, que deve ser realizada quando os sinais de desgaste são evidentes ou conforme o cronograma de manutenção preventiva. Entender o momento certo para substituir os retentores pode prevenir falhas inesperadas e garantir a continuidade das operações industriais. Uma substituição eficiente envolve não apenas a remoção e instalação de um novo retentor, mas também a inspeção cuidadosa do alojamento e do eixo para identificar possíveis causas de desgaste acelerado, como alinhamento inadequado ou superfícies danificadas.
Além disso, a atualização para tecnologias de retentores mais avançadas pode oferecer vantagens significativas, como maior resistência a ambientes corrosivos ou temperaturas extremas e melhor desempenho em aplicações de alta pressão. Fabricantes de retentores estão constantemente inovando em materiais e designs para aumentar a vida útil e eficácia dos produtos. Optar por soluções atualizadas pode resultar em custos de manutenção reduzidos a longo prazo e melhor eficiência operacional, evitando paradas não planejadas e aumentando a confiabilidade do equipamento.
Conclusão
Através deste artigo, exploramos diversas técnicas essenciais para a detecção e solução de falhas comuns em retentores, desde a identificação visual de desgaste até testes específicos de pressão e temperatura. Manter retentores em bom estado é crucial para a operação segura e eficiente de máquinas em uma variedade de indústrias. A implementação regular de inspeções e a aderência a um plano de manutenção preventiva são práticas fundamentais que ajudam a prolongar a vida útil desses componentes críticos.
Para garantir que você está utilizando os melhores produtos e obtendo orientação especializada, considere entrar em contato com a Vedacil. Nossos especialistas estão prontos para ajudá-lo a escolher as soluções de retentores mais adequadas para suas necessidades específicas e para fornecer suporte contínuo em todas as etapas do processo de manutenção. Visite nosso site para mais informações e para descobrir nossa gama de produtos de alta qualidade que podem ajudar a maximizar a eficiência e durabilidade de seus sistemas.